Refractory Materials Used In the Circulating Fluidized Bed Boiler (CFB)
Date:2016-08-17 16:04 From:Zhengzhou Sunrise Refractory Author:admin
Circulating fluidized bed combustion of coal is a new coal technology developed in nearly two decades and a major innovation of traditional grate furnace and pulverized coal furnace. Due to the high heat capacity, strong blending characteristics and low-temperature combustion of the materials, it can effectively burn lignite, bituminous coal and anthracite or low-grade fuels such as gas forming slags and petroleum coke. The boiler has good fuel adaptability and can burn a variety of coals in the same boiler. Circulating fluidized bed combustion can desulfurize flue gas by adding limestone and provides a way for the rational use of high-sulfur coal. However, since tail desulfurization technology is costly, it is difficult to be applied in small boilers. Circulating fluidized bed boiler is popular all over the world. After years of development, Circulating fluidized bed boiler with different structures and forms have been developed.
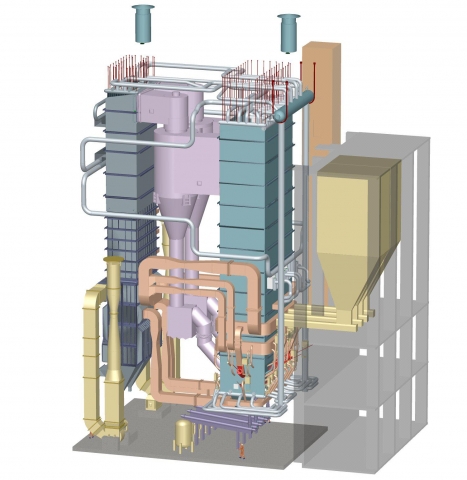
CFB boiler is different from traditional pulverized coal boilers. Bed materials rise along the furnace carried by flue gas and enter the separator through the upper outlet. In the separator, gas and solid phases are separated. After the separation, flue gas enters the tail flue. Solid particles return to the lower part of the boiler through the return valve.
During the operation of CFB, solid bed materials containing the fuel ash, limestone, and the reaction products flow in a closed high temperature circulation: the furnace - separator - return valve - the furnace. High efficiency combustion and desulfurization reaction happen in the furnace at 850-900℃. Except for the outer loop of the bed material in this circulation, bed materials also constantly flow in an inner circulation under the action of gravity. Therefore, wear is inevitably produced in the corresponding parts of the circulation. Wear not only affects the safe operation of the boiler, but also limits the full play of some advantages. Direct damage caused by wear and tear to the boiler is to reduce the thickness of metal pipe walls in heated surface which withstands internal pressure until bursting and shutdown. Wear increases costs of boiler operation and maintenance, decreases the utilization of the unit and cause huge loss. Currently, the common measure to prevent the wear of CFB is to lay thicker non-metallic, refractory bricks, castable or plastic materials.
Currently, there are many problems to be solved in the selection of refractory materials for CFB. Due to the different physical and chemical properties of various refractory materials, the selection of refractory materials is crucial, depending on parts, uses and characteristics of various boilers.
Erosion wear is the problem various CFB refractories have to face. Due to the characteristics of the boiler itself, in the operation, refractories are subject to the wear of solid bed materials including fuel, fuel ash, limestone, and the reaction products. Different coals have different chemical composition, volatile and ash and also have different wear effect on refractory materials. Also the structure of the furnace and flow rate is directly related to wear.
Temperature changes will cause expansion or contraction of refractory materials. If the expansion or contraction is restrained, stress can be generated inside the materials. Refractories are heterogeneous brittle materials. Compared with metal products, due to its small thermal conductivity and elasticity, low tensile strength, poor resistance to thermal stress damage, low thermal shock resistance and thermal shock cycle effect, refractories are prone to cracking and spalling and finally overall damage. It is another important reason for the early failure of CFB refractories.
The physical and chemical properties of refractory materials are very important. Generally the compressive strength, flexural strength, wear resistance, thermal shock resistance and reheating linear change of refractories are major assessment indicators. The high temperature compressive strength should be taken into consideration too. In particular, some castables are used at CFB combustion temperature. Since the combustion temperature cannot reach the sintering temperature, the castables have low strength. Such as high alumina cement castable, due to the increased amount of calcium, its strength reaches the peak after drying at room temperature and 110℃. But with increasing of the temperature, the strength drops and has the lowest value at 700-1100℃. There are many refractory binders that can only obtain a certain strength after sintered at 1200℃.
Unreasonable construction, installation and preheating are also one of the main reasons for the refractories damage. Most manufacturers have no refractory construction and installation experience and are not in strict accordance with the requirements of the design and the plant.
Currently, CFB refractories can be divided into three categories: wear-resistant refractory bricks, casting material, plastic material and mortar; refractory brick, castable and mortar; insulation refractory brick, castable and mortar. Usually, wear-resistant refractory bricks include phosphate brick and castable; silicate bricks and castable; silicon carbide brick and castable; corundum brick and castable; wear-resistant refractory bricks and castable; silicon nitride bonded silicon carbide products. But the results of these materials are not very satisfactory.
Phosphate bricks are bon burn bricks treated at low temperature (500℃). They are usually used at 1200-1600℃. It has been applied in the cement kiln for many years. Early CFB boilers are mostly built with phosphate bricks and phosphate castables. Since CFB is running in the range of 850-900℃, at this temperature, the physical properties of refractory are unstable and the wear resistance canno be fully realized. Phosphate castable has the same physical and chemical properties with bricks.
Sillimanite is a high quality refractory material. It can increase the refractoriness under load by 100~150℃ after added to refractories. The start changing temperature of refractories is 1450-1600℃ and the sintering temperature of sillimanite brick reaches this temperature, so it is an ideal wear-resistant refractory for CFB. But because the CFB combustion temperatue cannot reach the temperature of sillimanite castables, the wear resistance cannot be fully realized. Besides, sillimanite castables are expansive. All these affect the the application of sillimanite castables on the CFB.
Silicon carbide products have good wear resistance and good thermal shock resistance in non-oxidizing atmosphere at high temperature. They can form a protective layer of glaze after sintered at a temperature. The main reason is that there is a small amount of oxidizing atmosphere in the CFB combustion.
Corundum products used in CFB include white corundum, high-alumina corundum (also called Sub-white Corundum) and brown corundum. The main properties of corundum are high refractoriness, high bulk density and good wear resistance, but it has poor thermal shock resistance, which makes it difficult to be used in the CFB. Corundum castable frequently collapse in the course of use, resulting in shorter refractory life.