What are the factors that damage the blast furnace bottom?
Date:2020-01-06 16:06 From:Zhengzhou Sunrise Refractory Author:admin
Bottom furnace working conditions are extremely harsh, and its durability is a decisive factor in the life of a generation of blast furnaces. The bottom of the blast furnace has been under high temperature and high pressure conditions for a long time. According to the damage condition of the bottom protection after the blast furnace is stopped and the bottom temperature inspection during production, the bottom damage can be divided into two stages: at the beginning of the furnace, molten iron penetrates to float the bricks to form a pan-shaped deep pit. It is a chemical attack after the formation of a sintered layer.
Reasons for the bottom of the furnace: First, the bottom of the furnace is subjected to 10% to 20% of the wave slag iron, gas pressure, and gravity of the material column, which can be (2-5) x105pa / c㎡; the second is the brick of brick Seams and cracks. When the molten iron penetrates into the gap under high pressure, it is slowly cooled, and solidifies at 1150 ° C. Graphite carbon is precipitated during the condensation process, and the volume expands, which expands the slit courtyard. This is a mutual cause and effect, and the molten iron can penetrate deeply. Because the density of molten iron (7.1g / cm³) is much higher than the density of blast furnace clay bricks (22g / cm³), the density of high alumina bricks (23-3.7g / cm³) and the density of carbon bricks (1.6g / cm³). Bricks will float under static pressure.
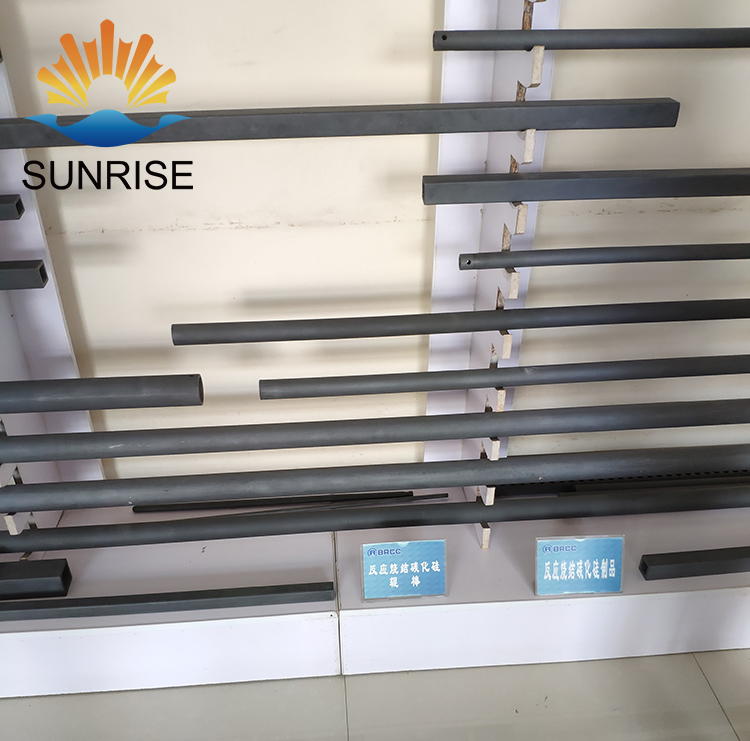
When the furnace bottom erodes to a certain depth, the erosion of the slag molten iron gradually weakens, and the brick lining under the pit is partially softened and recrystallized under long-term high temperature and pressure to form a grid layer with a thickness of about 700 ~ 1400mm. A lot thinner. The sintered layer is a whole with dense structure, disappeared brick joints, and high bulk density. Compared with the unsintered lower brick, the brick is compressed, the porosity is significantly reduced, the bulk density is significantly increased, and the brick is made after iron infiltration. The thermal conductivity is improved, and the heat dissipation ability is enhanced, so that the molten iron is solidified to move on the isothermal line (generally 1150 ° C). Since the bricks and bricks have been sintered into a whole in the sintering layer, the temperature of the molten iron at the bottom of the pit is lower, and the brick joint is no longer a weak link, so the sintering layer can resist the penetration of molten iron. The main reason for the damage of the furnace lining is the conversion of carbon in the molten iron to reduce the silicon dioxide in the brick to silicon, which is absorbed by the iron.
The damage to the bottom of the furnace is generally at home and abroad. The bottom of the erosion line is flat-bottomed, and the erosion depth is about 1.5 ~ 2.5m. The danger zone changes from the bottom of the furnace bottom to the peripheral wall, that is, the bottom wall of the furnace bottom is eroded more and more severely below the centerline of the iron mouth, and the erosion line is extended downward and outward to form a garlic head shape.
There is a ring-shaped brittle layer centered on the center line of the furnace. Some residual bricks have holes. This is because the molten iron penetrates into the brick to form a brittle layer. The inner part of the brittle layer is taken away by the molten iron. In addition, some bricks around the bottom of the blast furnace integrated with the central high alumina bricks, and the expansion rate of the high alumina bricks is larger than that of the carbon bricks. It is easy for the carbon bricks to be lifted by the high alumina bricks. The gap widens and molten iron penetrates.