Application of amorphous refractory material
Date:2017-12-19 16:53 From:Zhengzhou Sunrise Refractory Author:admin
The application of amorphous refractory materials, almost all areas of the editor of the furnace and thermal equipment and structures, and obtain significant economic results. As we all know, in all kinds of industrial sectors, the metallurgical industry has the largest number of kilns and harsh conditions of use. Refractory materials consumed account for about 60% of its total content.
In the metallurgical industry, smelting furnace and its ancillary equipment consume the most refractory material, its quality requirements are relatively high. In order to measure the refractory materials and metallurgical furnace process equipment and technical level, commonly used refractory unit consumption said. The unit consumption refers to the ratio of the total amount of refractories metallurgical furnace and steel production. Refractory material consumption abroad per ton of steel is generally below 20kg. Japan's steel consumption is about 11kg, China is about 32kg. Shanghai Baosteel tons of steel consumption is about 15kg, has reached the world standard. Its unit consumption continued to drop. In 1995, it was 10.9 kg per ton of steel. Stereotypes were continuously reduced while that of monolithic refractories increased. By 1988, 5.9 kg was consumed per ton of steel for shaped products and amorphous refractory materials. By 1995, amorphous refractory materials consumed 6.4 kg / tonne of steel and 4.5 kg was shaped. This once again shows that in the steel industry, monolithic refractories occupy an extremely important position. In China, in order to reduce the consumption of refractories, in addition to improving equipment, to achieve large-scale, to improve the level of automation and continuous casting ratio, the development of high-quality refractory bricks and to change the variety of structures, should popularize the popularization of amorphous refractories, it is imperative, and Get more with less effort.
(A) ironmaking system
Ironmaking systems include sintering, coking and high aluminum and their ancillary equipment. Belt sintering machine Ignition of refractory plastic and clay with castables on-site production, or phosphate refractory castable prefabricated blocks hoisting, the service life of 3 to 6 years. When the line ignition device is used, the top of the furnace is pressed down more, the working conditions of the furnace become better, the lightweight high-strength refractory castable or refractory fiber and its products can be used as lining, and the better effect is obtained; , Overlay and the door and other parts with refractory castable watering, burner damage, then spray paint repair. In addition, CDQ equipment is also used heavy or light refractory castables; blast furnace is a continuous production of ironmaking equipment. Small-scale blast furnace used aluminate cement and high-alumina refractory castable prefabricated blocks to lift masonry, and is now commonly used in cement-bonded aluminum carbon brick masonry. Large blast furnace water wall with silicon carbide castable lead to the furnace floor and the surrounding brick cracks are castable refractory and silicon nitride filler, when the lining is damaged with refractory material and fire-resistant spray paint repair, in order to extend the service life , So that the furnace reached 10 years or even 15 years. Blast furnace taphole generally scattered bulk Al2O3-SiC-C gun stem blockage, iron can be guaranteed stable iron outlet, the operation is normal. Blast furnace tapping the original use of fire-resistant ramming material ramming, ditch material iron consumption of about 1.1kg. Now using low porosity and dense refractory castable pouring, an iron throughput of about 100000 t, a generation of gully age total iron volume of about 900000 t, refractories tons of iron consumption less than 0.38kg. At the same time, self-flowing refractory castables and bake refractory castables have also been applied to the blast furnace hooks.
Hot blast stove is a key subsidiary of iron blast furnace equipment. Medium and small blast furnace stove lining, refractory castable precast block masonry. Hot stove burner available refractory castable block prefabricated masonry or on-site watering, the ball top is refractory castable watering work lining. Large-scale hot-blast furnace body shell by the shell of the first layer of bulk density of about 1.3g / cm3 of light spray material, the ball is sprayed with a layer of acid spray paint, the formation of the overall lining, corundum refractory castables and other materials, the scene Watering, get a better use of the effect; torpedo-type hot metal and iron mixing furnace generally partial or full use of refractory castable, refractory spray coating can also be used to repair, the use of better
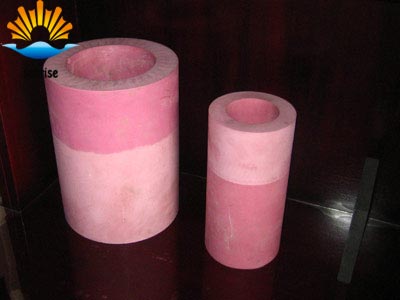
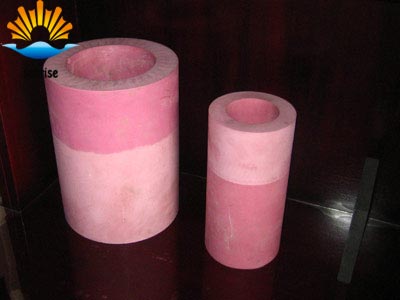